Sure, the right construction quality management software can increase profits and customer satisfaction while reducing defects. But, have you considered how much money you’re losing by not having quality management software, and how much of that can you get back with good quality management software? Business is business, so let me show you the money. Then you’ll see how much quality issues are costing you.
What Makes Quality Management Software so Effective?
There are actually three reasons why construction quality management software is so effective:
1- Organizational culture: The way you manage your business practices can establish a positive or negative culture. Quality management software can help you build a culture that emphasises quality.
2- Efficient communication: The more efficiently you can communicate, the more you can get done. Quality management software can help you quickly and easily share information across your company, saving you hours and hours of time.
3- Direct connection to profitability: Many business owners mistakenly assume that improving quality is a cost that negatively impacts their profits. However, the opposite is
true. By implementing quality management software, you can see the direct connection to your profits
See the dollars
Quality control issues, often referred to as 2nd-time quality, encompass a spectrum of challenges in various industries. These issues can range from something as tangible as the improper installation of a window to more abstract concerns such as managing the rescheduling of work. Ensuring high standards in these areas is where quality management system software comes into play. It acts as the linchpin for effectively addressing and preventing such issues.
Additionally, audit management plays a vital role in ensuring adherence to these standards, while supplier quality assurance is crucial for maintaining consistency throughout the supply chain. Ultimately, a robust quality control system, supported by audit management and supplier quality, serves as a critical component of risk management, as any defects or lapses in quality can have significant financial repercussions.
If you take the next 5 minutes to work out the dollar amount that your company loses in time alone, you'll start to understand how expensive 2nd-time quality can be. Taking corrective and preventive action soon enough will save you unnecessary headaches.
Here’s how to figure out how much time quality control issues are costing you in wages alone:
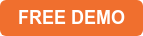
Sketch an organization chart that lists job positions for all employees from President to your workers.
- For each role, ask yourself what percentage time does each person spend dealing with quality problems, what a typical annual salary is, and how many people you employ in the role.
- For each role, multiply the three figures.
- Add all these numbers together.
Below are some ballpark numbers for the cost of time spent on quality control issues. The Percentages of Time Spent are averages based on data from construction companies I have worked with over the years.
GC or Homebuilder
Position | Percent of Time Spent | Salary | Number of Employees | Annual Cost of 2nd Time Quality |
President | 10% | $150,000 | 1 | $ 15,000 |
Project Managers | 25% | $125,000 | 2 | $ 62,500 |
Superintendents | 50% | $100,000 | 6 | $300,000 |
$377,500 |
Speciality Contractor
Position | Percent of Time Spent | Salary | Number of Employees | Annual Cost of 2nd Time Quality |
President | 10% | $150,000 | 1 | $ 15,000 |
Project Managers | 10% | $125,000 | 1 | $ 12,500 |
Superintendents | 50% | $100,000 | 2 | $100,000 |
Crew Leaders | 25% | $ 40,000 | 10 | $100,000 |
Crew Members | 10% | $ 30,000 | 40 | $ 12,000 |
$239,500 |
Your company's annual cost of quality management issues will differ from my ballpark numbers. In fact, you can use quality management data to help you with your numbers. The actual cost is much greater when you consider material waste; impact on build time, future sales and reputation; as well as warranty issues and possible litigation costs. Nonetheless, if you are like most construction companies, the annual cost of quality is considerable.
Connect quality directly to profitability
In the realm of quality planning, each successful outcome directly impacts profitability. The more consistently things go according to plan, the greater your potential for profit. By adhering to the straightforward principle of first-time quality, you pave the way for sustained profitability.
Your quality management software should serve as more than just a tool for identifying quality issues; it should also be a means of recognising instances of first-time quality and attributing them to specific contributors.
This becomes particularly crucial for businesses in the medical device industry, where strict adherence to quality and compliance processes is non-negotiable. Additionally, effective supplier quality management plays a vital role in maintaining these high standards, ensuring that every link in the supply chain contributes to overall quality and profitability.
Develop an accountable culture
If you set your company up with a top quality management software to connect quality issues to the responsible parties, you will know who is responsible for the quality issues and what had to be done to address them.
Your subcontractors and crews will soon realize that their oversights, errors, and very importantly, their good performance, are visible and they will take more pride in what they do. Without a quality management system and a decent quality management software, all you often know is that the work was finished, but not if it was done right the first time.
Inspections, scores, and checkpoints can help develop a job site culture focused on getting it right the first time, which will save everyone time and money.
Understand where to focus your time and energy
Effective quality management software is a critical tool in the pursuit of continuous improvement. It serves as your guiding compass, directing your time and energy towards areas that warrant attention.
In the quest for efficient management, understanding the frequency and severity of recurring issues is paramount. By meticulously tracking subcontractor and crew performance, you gain a deeper understanding of where your team requires support to achieve success.
In your pursuit of collective success, it becomes imperative to discern the nature of the assistance required when a particular area calls for your attention. This assistance may take various forms, including training, adjustments to work procedures, enhancements in materials and equipment, or even seeking additional expertise.
This holistic approach holds exceptional significance, especially in sectors such as medical device manufacturing, where the precision of document control and the integration of enterprise quality management are pivotal components within comprehensive quality management systems.
It is helpful to have a quality management system that can help your teams discover problems early and address them right away but having an overall view of all your projects can also be a huge help. While a small problem on a job might feel like an annoyance, if this same problem happens on all your jobs, it might be costing you more than you realize.
Defects should not be part of your normal business; consider them problems – problems can be avoided.
Do more business
When you show clients how your quality management processes are managed using a software system, you can help them feel more confident in your work.
You can show your ability to closely monitor quality, discover problems quickly, and address them right away. You need less oversight. Clients will see the value in this. How much more business could you do as the preferred contractor?
Get better bids from subcontractors
Subcontractors and suppliers will learn that things go smoothly on your projects. When they know they can get in, get to work, and get done, you avoid the “hassle fees” they build into other bids.
Conclusion
If you put your mind to it and have the right tools, how much money could you get back in the next year? 10%? 25%? 33%? What about in two years? Where could you be in three years?
Quality could be your company’s biggest profit enhancement opportunity, and it has been hiding in plain sight.
A quality management system can help. If you’d like to learn how FTQ360 construction quality management software can increase your profits and reduce problems with your projects, contact us.