Handover of subsystems from the construction team to the commissioning team can be one of the most complex aspects of project commissioning. But it doesn’t have to be that way if meticulously planned for in advance.
It goes without saying that the construction plan needs to be completely aligned with the commissioning plan. This is so that all portions of the project are ready and available when you need them to support the overall commissioning and start up sequence.
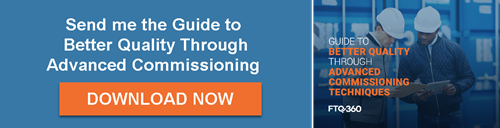
Today’s projects are more complex than ever which makes the handover process even more challenging than it used to be. With very specific information to be managed during the handover process, paper and spreadsheets are not capable tools to manage a multitude of details. There are now far superior options that will streamline the process and make sure that every important detail is not lost in the process. Today’s CMS tools need to be leveraged to manage the vast amount of information that exists within projects.
Construction Quality Processes Leading up to Handover from Construction to Commissioning
The commissioning phase of your project will only be successful if proper Quality Assurance / Quality Control processes are implemented during installation activities that precede commissioning. And a properly implemented Quality Management System (QMS) during construction is paramount to achieving success.
Multiple Inspection and Test Plans (ITPs) are required as installations are completed. This quality control function generates a significant amount of paperwork that needs to be tracked and archived for further reference. While this has been done using hard copies of ITPs in the past, the sheer volume of information available on today’s projects makes this manual tracking method unmanageable.
Manually completing each ITP in the field can present errors as handwriting may be illegible or data gets lost in the process. The details matter during commissioning, and a cable that was missed during installation but not identified during the QA/QC process can cause significant delays during critical path commissioning activities.
The QA/QC processes leading up to handover will identify deficiencies to be rectified before commissioning can start, or that must be completed prior to handover to the owner. There will be lots of small details to manage and track and this can only be done accurately using software tools to ensure nothing gets missed. With many items being tracked through construction and the building commissioning phases, today’s software tools are key to ensure the transition between project phases goes smoothly.
Mechanical Commissioning
For each mechanical completion, a set of ITPs must be in place and be completed by the construction team to confirm correct installation and quality requirements are being met. A list of ITPs is included in each stage of mechanical completion, and these will be reviewed during signoff of each one to confirm all prerequisites have been met for the system. At that point, installation is complete and ready for commissioning.
Each mechanical completion also includes all the construction documentation such as O&M manuals, red-line drawings, quality records, etc. Some of this information is required during project commissioning and other information is required by the owner at project completion. Either way, there is a significant amount of information to be gathered and tracked.
In the past, information from the construction team would be submitted by paper or email. At some point later in the project, all the information for turnover to the owner is searched for and gathered into turnover binders. Hard copies or electronic files of each turnover binder are then given to the owner. This can be a significant task at the end of the project to search for all required documentation and format into a presentable package.
Unfortunately this task is often de-prioritized. It’s habitually left too late in the project and the project team is eager to move onto their already scheduled next project. It ultimately ends up being given to an inexperienced summer student to take care of. Don’t fall into this bad habit, there are much better solutions that exist to enable the commissioning team to provide higher quality products to the owner at the end of the project.
With today’s software systems, handover of documentation at mechanical completion is simplified. As documents are received and catalogued through construction and commissioning phases, the information is automatically organized within the software systems.
At the end of the project, once all documentation is received, it is as simple as clicking a button to generate each turnover package for handover to the operating team. This saves months of effort and provides much more complete documentation that can be used for the life of the new assets.
Create an Integrated Construction and Commissioning Schedule
The list of milestones for each mechanical completion forms the critical handover dates required for each subsystem, and these are included in the project schedule. This list of milestones provides guidance to the construction team of how to sequence the work and plan construction activities. Any milestone dates that cannot be achieved need to be identified by the construction team well in advance so that options can be discussed with the commissioning team to determine how to best plan the work.
The integrated construction and commissioning schedule is reviewed frequently, maybe monthly at the beginning of construction, and increasing in frequency as mechanical completion milestone dates are approaching. Any delays to construction activities need to be closely monitored to determine if there will be impacts to the commissioning sequence, and if so, how can delays be mitigated.
When separate construction and commissioning schedules are maintained, this collaborative discussion becomes much more difficult. Without an understanding of impacts of construction delays on the commissioning sequence, the project team has no ability to evaluate mitigation options. This list of critical handover milestone dates needs to be closely monitored regularly.
While evaluation of schedule impacts has been somewhat of a manual process using the software packages on the market, today’s commissioning software tools now include this forecast function and can automatically identify impacts to the project in-service date. With advance notice of potential issues, the project team can act to proactively address the issue and avoid costly delays to the handover process.
Pre Commissioning Activities
ITPs and mechanical completions must be defined well in advance so that the commissioning team knows what they are receiving. As well, pre commissioning checklists need to be defined in advance so that testing can take place without delay once received from the construction team.
There needs to be documentation defining the scope of construction versus the scope of commissioning. For example, if the project commissioning team was expecting the construction team to do point-to-point checks, but at mechanical completion it is discovered this was not done, this will cause project delays to have to then go do the pre commissioning checks on cables.
Pre commissioning checklists are required to guide the team on what checks need to be completed and who needs to do them, and checklists have been used for decades to verify electrical and mechanical equipment. Over the years, the checks to be done on standard equipment has not changed, yet each project is required to create a new checklist for the project.
But why? Let’s use a simple example. The checks to complete during a pump initial run-in typically are to measure vibration, current draw, inlet and outlet pressure and flow rates. These are measured for 3 points on the pump curve.
These have been the same set of checks to perform on a pump for decades. So why do we re-create this checklist for each project? Instead, a standard list of checks for typical equipment is needed.
And today’s software packages can offer the ease of drag and drop to include these checks in project checklists. There is no longer the need to locate a previous project’s checklist and change the title on the document for the new project with the same list of checks. These resources are now available to make checklist creation much easier rather than having to re-create each time for the same equipment on each project.
Taken one step further, data is recorded directly into software packages. A hard copy of the checklist is no longer required in the field with data entry errors. Technicians in the field enter information directly into online checklists where it is recorded and evaluated against pass/fail criteria. Once completed, checklists are archived for inclusion in final turnover packages to the owner.
Coordinating Construction and Commissioning Work
Construction and commissioning services are likely to overlap on most projects. It is unlikely that all construction is 100% complete and the construction team has demobilized from site prior to the commissioning team becoming involved on site. Some systems will start being tested by the commissioning team while other subsystems are still under construction.
Work in this situation needs to be closely coordinated. It would be unsafe to have one group energizing systems for the first time while another group is still installing it. Formal mechanical completion and handover documents signify the transfer of care/custody/control of a subsystem from one group to another. And this is important to identify which group is responsible for determining the daily activities to be taking place on a particular subsystem.
Once a subsystem has been handed over to the commissioning team, they will identify the boundary isolations that need to be established and the LOTO requirements that need to be in place. The LOTO and PTW processes established on site need to be followed by all groups.
And the construction team will need to work within the established boundary isolations to ensure they stay clear of any pre-commissioning and commissioning activities on an adjacent subsystem. Any changes to boundary isolations need to be communicated and coordinated in advance to ensure all groups are aware of what work can take place safely.
Final thoughts:
If not planned for in advance, the construction to commissioning handover process can be quite challenging. There are lots of details to determine so that the handover process goes smoothly, starting with a properly implemented QMS. And the amount of information and details on today’s project requires more robust processes than using paper and spreadsheets.
Don’t assume that the details will just be figured out at the time of handover – any items that are missed between construction and commissioning phases will cause delays to the project, unsafe working conditions, or incomplete systems. The construction team and commissioning team need to work closely together to plan for and execute a smooth handover from one group to the other.
A Better Way to Manage Commissioning
Many commissioning engineers get it wrong because they use antiquated methods to manage the commissioning process. Paper and Excel spreadsheets may have been the only options available years ago but are far inferior now. Best practice commissioning dictates the use of commissioning software to manage the entire process.
FTQ360 is a cloud commissioning platform to improve and streamline your commissioning process so that you get it right the first time. It starts with the end in mind by collecting documents and reports in an organized way throughout the commissioning process so that you are always prepared for a fast and easy closeout. Automatically format and organize all inspections and tests into a turnover package.
With FTQ360, upfront planning of inspections and tests for specific equipment and systems and schedule management are baked right into the process. It also comes with a large library of fully customizable checklist templates to help you save time.
Communicate issues in a managed process from discovery to resolution and tie all tests and inspections to specific equipment tags, sub-systems and the overall system.
Generate easy-to-read inspection reports with proof-positive compliance documentation at the touch of button. See the big picture with dashboards and graphical reports, then focus on the details. View reports online or schedule them to automatically run and email.
FTQ360 is available as a mobile and web application. For more information on how FTQ360 can improve your commissioning process, book a free demo today.